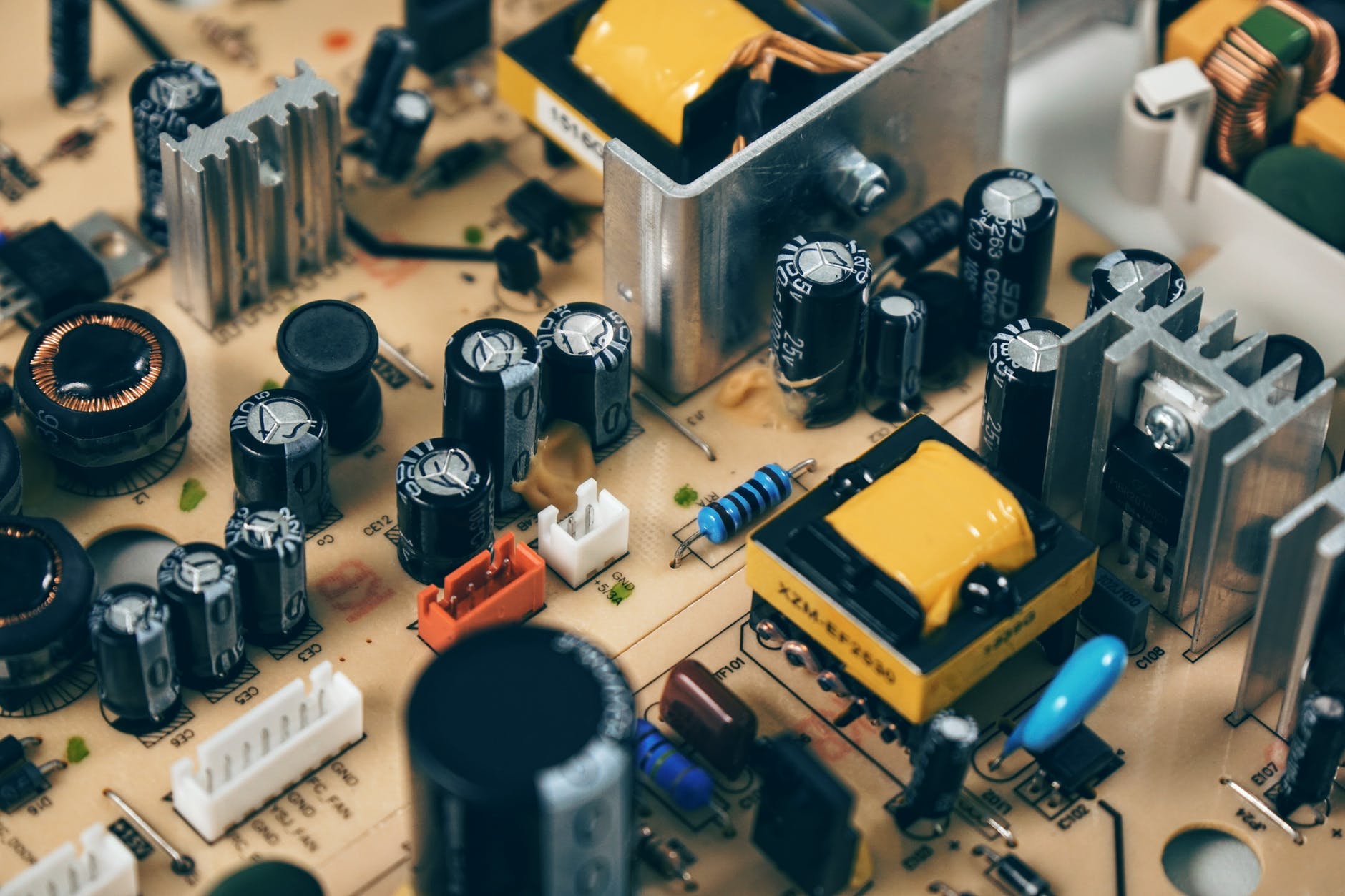
It’s important to look at this as a specific component when implementing a warehouse management solution within your business. Despite all the improvements we’ve had in the software and the ability for us to produce a solution that makes it easier, faster, and more efficient for our customers to be able to complete warehouse management processes, hardware is an extremely important part and there are many factors to look at when choosing the right device for your business.
Some of these include things such as:
- Cost;
- Compatibility or operating system in which they run;
- Scan engine which is extremely vital to the speed at which they can actually scan the specific items for the solution to be able to start determining what they are;
- Drop grade;
- Ability to be disinfected; and
- Dust specs.
Factors to Consider
All of these specific factors are important from a point of every single device that you look at. There are also other factors depending on the specific industry which you’re in. Things such as whether to include keypads on the devices themselves are also important depending on whether people will be using gloves or not using gloves throughout the warehouse, whether you’d be in a colder environment where that is necessary or whether it’s possible to take them off.
It is also important to look at the different components of the device itself, including being 4G capable or only using WLAN for specific devices. For us, the extremely important part of our solution is the ability to run online and offline. It’s not necessary to always be connected. This is a great advantage of the Cloud Coders solution but also plays into which device would be needed throughout the business.
The drop grade or dust spec is also extremely important depending on the industry. If it is a fashion retailer, for example, something like the CT40 will be a fantastic device. If you’re looking at a business that does manufacturing or has large and heavy products where devices may fall or be dropped onto these harder devices, then it’s potentially important to look at an upgraded device over that — something such as an EK65 or perhaps the CT60.
Additionally, there are also important decisions to be made around charging processes, such as using a battery dock where you take out the batteries and charge these individually. Put them back into the device or a device dock where you would put the devices in without removing the battery. In the battery docks, you can use a process called hot-swapping, where you have batteries always charging only to be put in when needed. For the docks, an important way to store the devices so you can see that all devices are back at the end of the day.
For scanning and how this is done in an ergonomic way for the warehouse staff, whether that’s using something such as a ring scanner, either Bluetooth or sled based, we’d be looking at a scan handle itself, which allows you to attach a pistol grip to the device itself and then use that to scan. There are also things that can help ensure the longevity of the devices. Things such as rubber boots and cases, as well as more protection for the screens themselves.
Hardware is a topic that we can continue to go into in a lot of detail around specific devices. But it’s always important to remember some of those key factors that were mentioned when thinking about what hardware fits best with your business.
If you would like to learn more about how Cloud Coders can improve your Warehouse Management processes then please get in touch. We’d be happy to take you through the most viable solution to determine where it will benefit your business and give a great return on investment for the implementation of your warehouse management solution. Likewise any feedback or questions that you have about our solution, feel free to get in contact for more information.